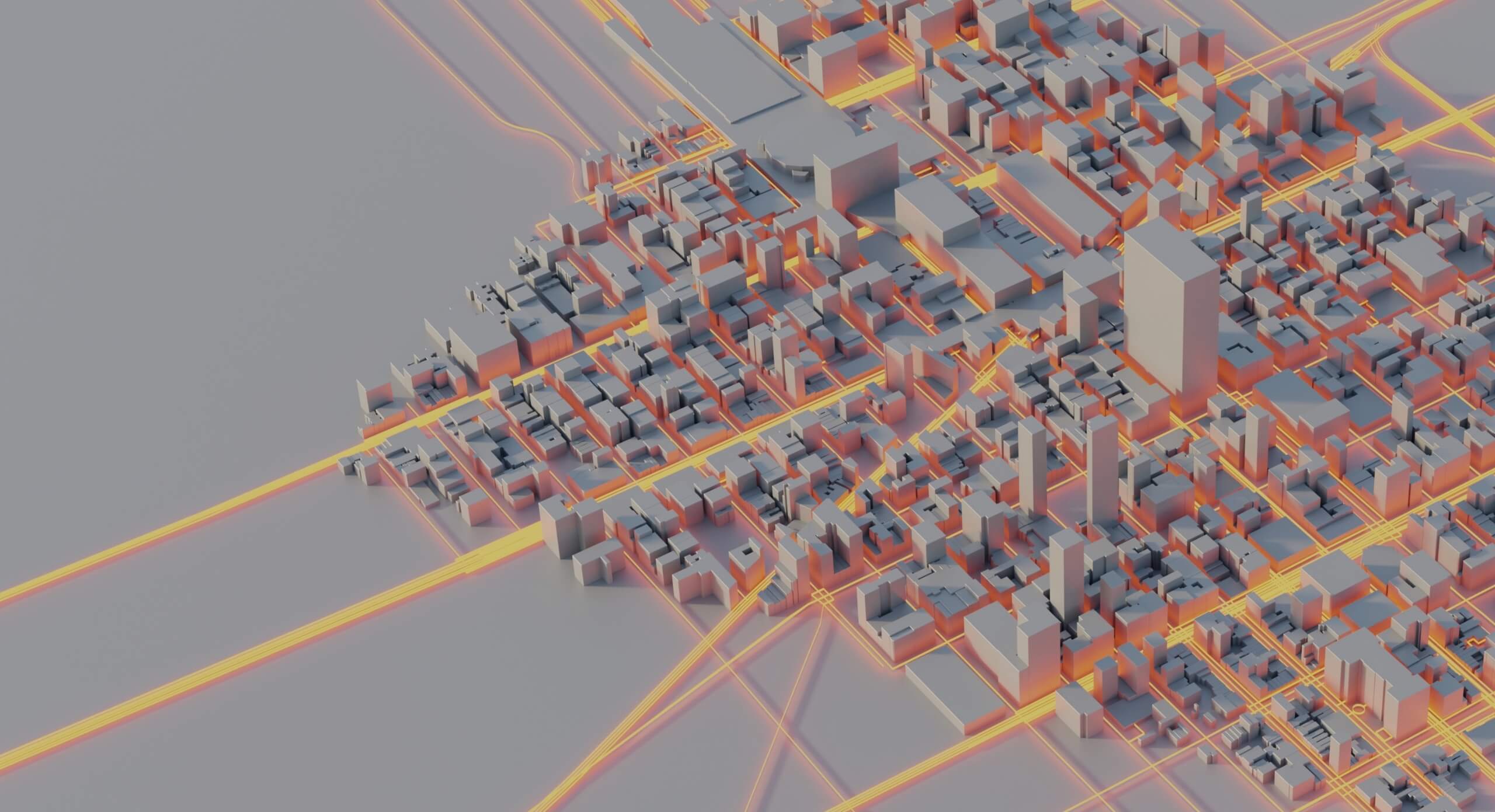
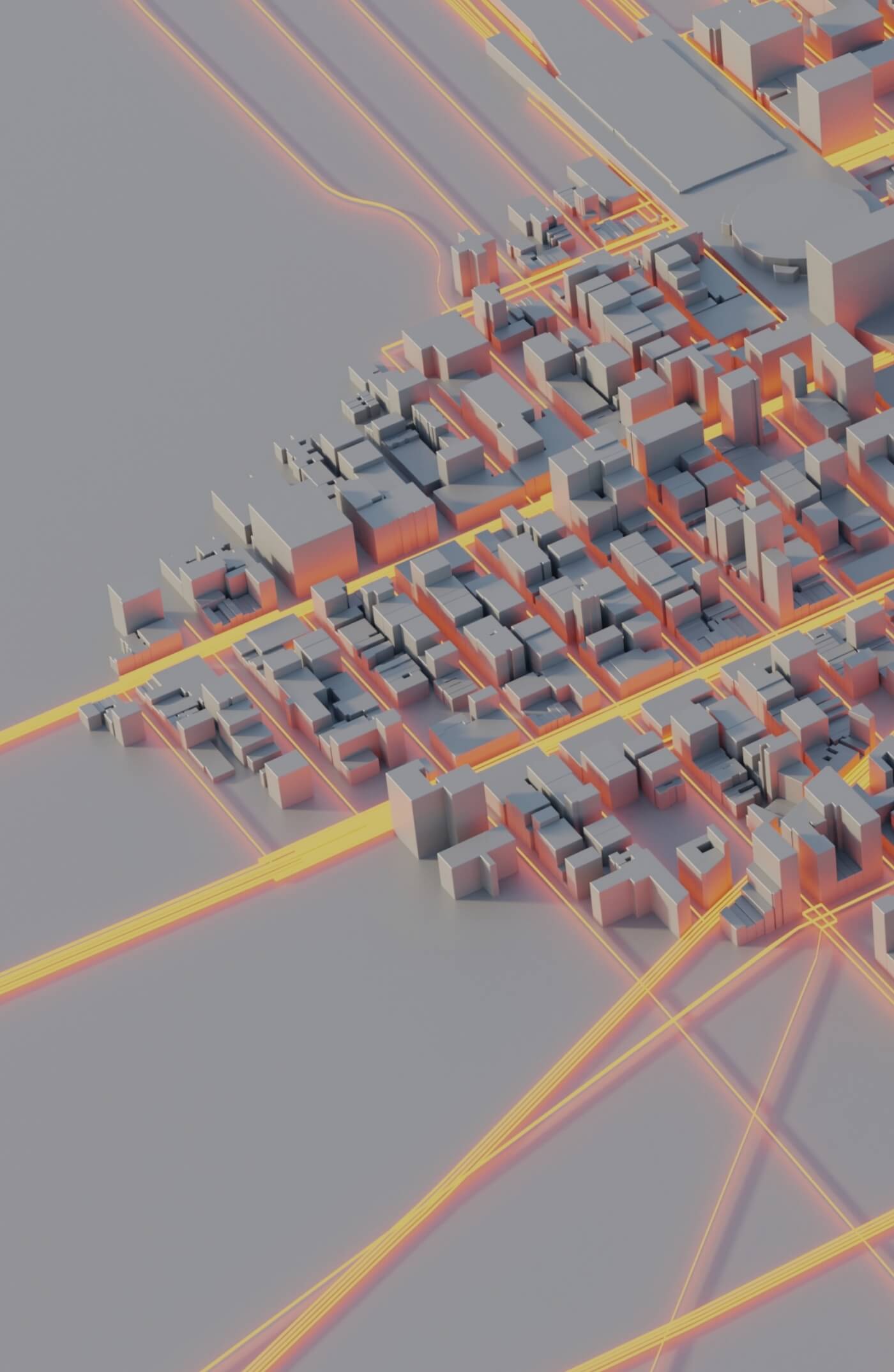
Business
Our Service Lines
Total
Quality
Solutions
Our
Strength
We provide one-stop
reliability test/analysis technology that
contributes to improving
development efficiency.
We value our passion as engineers and the accumulation of objective data, and provide our customers with "satisfaction" and "impression" by improving the "safety", "environment", and "comfort" of products. We aim to be a company that can contribute to society.
It all started with on-site improvements at factories and technical guidance. Currently, we provide "Total Quality Solutions" ranging from analysis, reliability testing, sample preparation, reproducible experiments, to contracted research. In these "Total Quality Solutions", experts covering academic fields such as chemistry, physics, metallurgical engineering, electrical engineering, and electromagnetics work together with engineers experienced in design, development, production technology, and quality assurance in the field of design and manufacturing to solve problems.
There are many companies specializing in specific fields such as analysis or reliability testing. However, our strength lies in our ability to conduct comprehensive analysis and research across all fields. We not only investigate the root causes of defects and failures that our customers face but also have the "capability" to delve into improvement proposals to enhance product safety, environmental friendliness, and comfortability.
Through our extensive range of operations, we are also engaged in new technological developments for electronic components and semiconductors, leveraging the data and insights accumulated over time. This is why we take pride in the fact that leading Japanese companies, which you often hear about, consult with us, a small to medium-sized enterprise, on matters of technology and quality.
Our
Services
-
Analysis
We provide accurate and prompt analysis services that not only evaluate products but also offer solutions to address any issues.
-
Failure Analysis
We use our accumulated advanced know-how and the latest equipment to thoroughly investigate the cause and effect of defects.
-
Laser Processing
Compatible with ultra-small and thin mobile electronic devices. To the submicron domain, to the nano world.
-
Cross-sectional Polishing/CP Processing
Our polishing center has a monthly production capacity of 10,000 pieces. We provide reliable technical capabilities based on our track record.
-
Power Cycle Test
Expertise and achievements have been cultivated through over 200 contracted tests annually. We also have 50 units of water-cooled power cycle test machines ready.
-
Reliability Test
Absolutely, it's the lifeline of product development and manufacturing. We propose a total solution that ensures high reliability.
-
Reserch and Development(Mounting technology/board/surface treatment)
We offer proposals for new techniques and materials demanded by the market, utilizing information and technical expertise gained through analysis, inspection, and experimentation.
We ensure
the fairness of tests and evaluations,
and we have established
a system to meet our customers' requirements.
“Trusted” by customers with JNLA certification
- Providing accurate data
Qualtec is registered and certified by the National Institute of Technology and Evaluation (NITE), an incorporated administrative agency, as a testing facility that complies with ISO/IEC 17025 under the Industrial Standardization Law Testing Operator Registration System (JNLA). Our technological capabilities have been recognized internationally, and we are contracted to perform numerous tests and inspections, including analysis and reliability evaluation of electronic and automotive components. We will continue to maintain and expand this certification to ensure fairness.
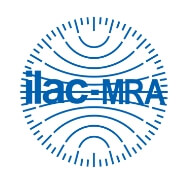
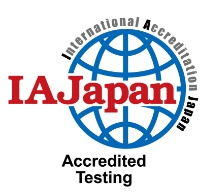

We have obtained certification in 5 categories.
The names of the testing methods are as follows.
Category No. |
Test method |
Notification |
---|---|---|
215 |
Plating thickness test |
JIS H 8501 |
40 |
Insulation test |
JIS C 5012 |
128 |
Electrical components |
JIS C 5012 |
106 |
Durability and |
JIS C 5012 |
156 |
Automotive parts |
JIS D 1601 |
In addition to the above, our strengths lie in our being an "independent testing company" and our ability to provide "Total Quality Solutions" that respond to a wide range of customer needs on a one-stop basis, which is achieved by having a large testing lineup. In response to the growing importance of evaluations and tests conducted by neutral third parties, we provide accurate data quickly and at reasonable prices. We improve the quality of our customers' products and parts, contributing to improvements in "safety", "environment", and "comfortability".
From a world of zero defects
to creating "Future Quality"
In addition to the "Zero Philosophy", which pursues so-called absolute quality, such as factories with zero defects and products with zero failures, there is also "Future Quality" that regenerates nature, such as cars that purify the air and smartphones that are made from materials that can be returned to the earth. Our analysis/evaluation, reliability testing, research and development, and microfabrication technologies provide total support for the creation of products with these features.
Our Zero Philosophy
Click to see the detail
-
The Pyramid Structure of Zero
In general, setting the goal of higher-level concepts before achieving the goals of lower-level concepts often results in neglecting the lower-level concepts in the factory site and failing to produce the expected results. In the theme of environmentally friendly manufacturing, aiming for "Zero Emissions," the highest level of zero, requires thorough environmental awareness and the practice of daily small-trouble-zero activities. Ignoring minor issues and not engaging in daily improvement activities in factories will make it impossible to achieve zero defects or zero failures, and concepts like stockless production will remain distant dreams.
-
If It Is Possible,
It Will Surely Happen!People who leisurely hold a coffee cup on their desk are not suitable for the manufacturing industry in the first place. The minimum requirement for a production worker is someone who can immediately imagine a situation where a coffee cup falls to the floor, breaks, and spills coffee all over the floor, and immediately shouts, "This is dangerous!" We must be prepared to take these actions, no matter how unlikely they may seem. For example, if there is cigarette ash lying around the ashtray, we think that it is the same as a fire breaking out in that room. If you make this kind of training a habit on a daily basis, you will develop the ability to see the possibility of small dangers and avoid accidents.
-
Heinrich's Law
Heinrich's Law, born from the analysis of data from life insurance company investigations, states that behind one major accident, there are approximately 29 medium-sized accidents, and further, behind those, there are 300 small accidents. This famous law succinctly expresses the essence of various phenomena involving human beings and serves as a bible for manufacturing sites. When applied over time, it reveals that major accidents do not occur spontaneously; rather, there are numerous small accidents leading up to them. In other words, the future is predictable. For those of us who absolutely want to avoid accidents or defects, this law is a blessing in disguise.
The most fundamental principle of zero-defect manufacturing is to cultivate a sensitivity that does not overlook small changes. By improving each small trouble one by one, it is believed that significant goals can always be achieved. -
The factor of variation
is not the 5Ms,
but rather just 1M (Man).In conventional quality control, the cause of defects is variation, and these variations are said to be caused by five factors (Material/Method/Machine/Measurement/Man). However, we believe that the only variation that directly leads to defects is 1M (Man). There are places where equipment deteriorates and breaks down, and materials change, but if you inspect them beforehand and perform maintenance and inspections properly, you can restore them to normal conditions. In other words, defects can be prevented if humans do not make mistakes or cut corners.
In zero manufacturing, it is important to thoroughly suppress variations in 1M (Man). To achieve this, we must first start by reviewing our systems and environment and reforming our factories so that no one can make mistakes. -
Digital 0 and
Time ConceptsAnalyzing a graph of defect rates over time isn't effective for improving factory performance. What matters for achieving zero defects is distinguishing between occurrence ("1") and non-occurrence ("0"), along with managing the time interval between them. Zero activity involves not just eliminating occurrences but also extending the interval between them.
Level I (Achieved zero defects for just one day)...Worker's mood
Level II (achieved zero defects for just one week): Motivation of manufacturing manager
Level Ⅲ (achieved zero defects for just one month): Efforts of engineers
Level IV (achieved zero defects for only 3 months): Professional teamwork between manufacturing managers and engineers
Level V (Achievement of zero defects for one year)...Thorough basic activities by amateurs
Level VI (achieving zero defects for 10 years): Fully automatic system with computer monitoring?
Zero manufacturing does not involve lowering the defective rate, but rather eliminating defects or extending the interval between defects (0 or 1). In general manufacturing processes, when focusing on process defects (defects before shipping inspection, not market complaints), "not producing the same defect for one year" is an important guideline for developing zero activities. -
0 Can Be Devided by the 0 That Can Be Achieved!
A phenomenon can be decomposed into its constituent elements, and these decomposed elements can be further broken down into elements of lower-level concepts. Phenomena have a hierarchical structure. On the other hand, phenomena are results of something, and there are factors that govern their causal relationships. The elements that constitute phenomena also have factors that are in the same causal relationship. In other words, phenomena can be broken down into a hierarchical structure over time, and if the higher-level phenomena exclude the lower-level factors, they will no longer occur. Causal relationships are not limited to direct ones. There are statistical causal relationships, logical causal relationships, and cases where all lower-level factors are involved.
Applying this concept to zero-defect manufacturing, thoroughly decomposing the theme of zero defects or zero breakdowns reveals that factors related to humans are controllable, and zero can be achieved by eliminating these problems. Meticulous factor analysis and the diligent effort to eliminate these factors are the essence of zero activities, and there is no other way forward.
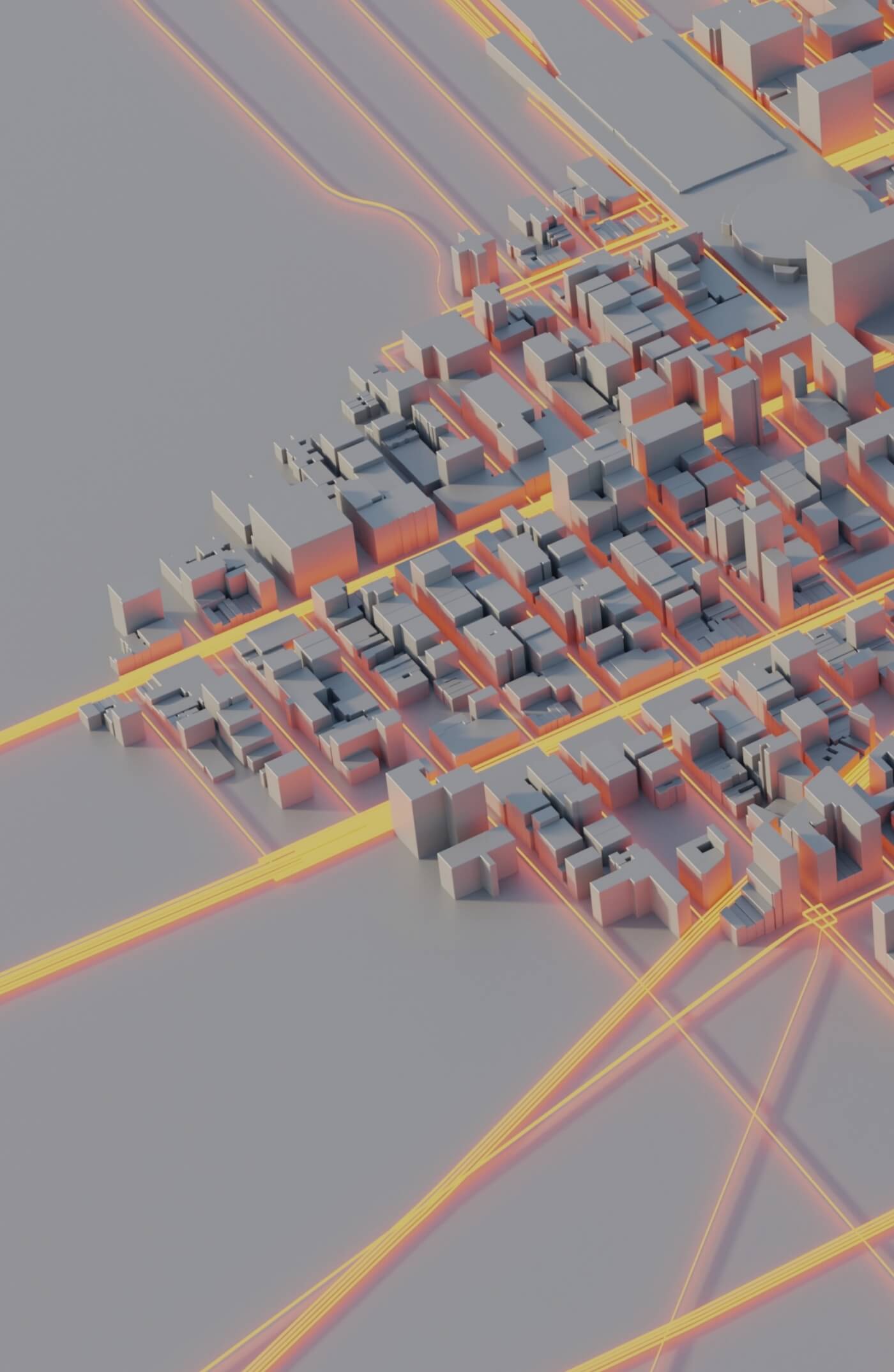