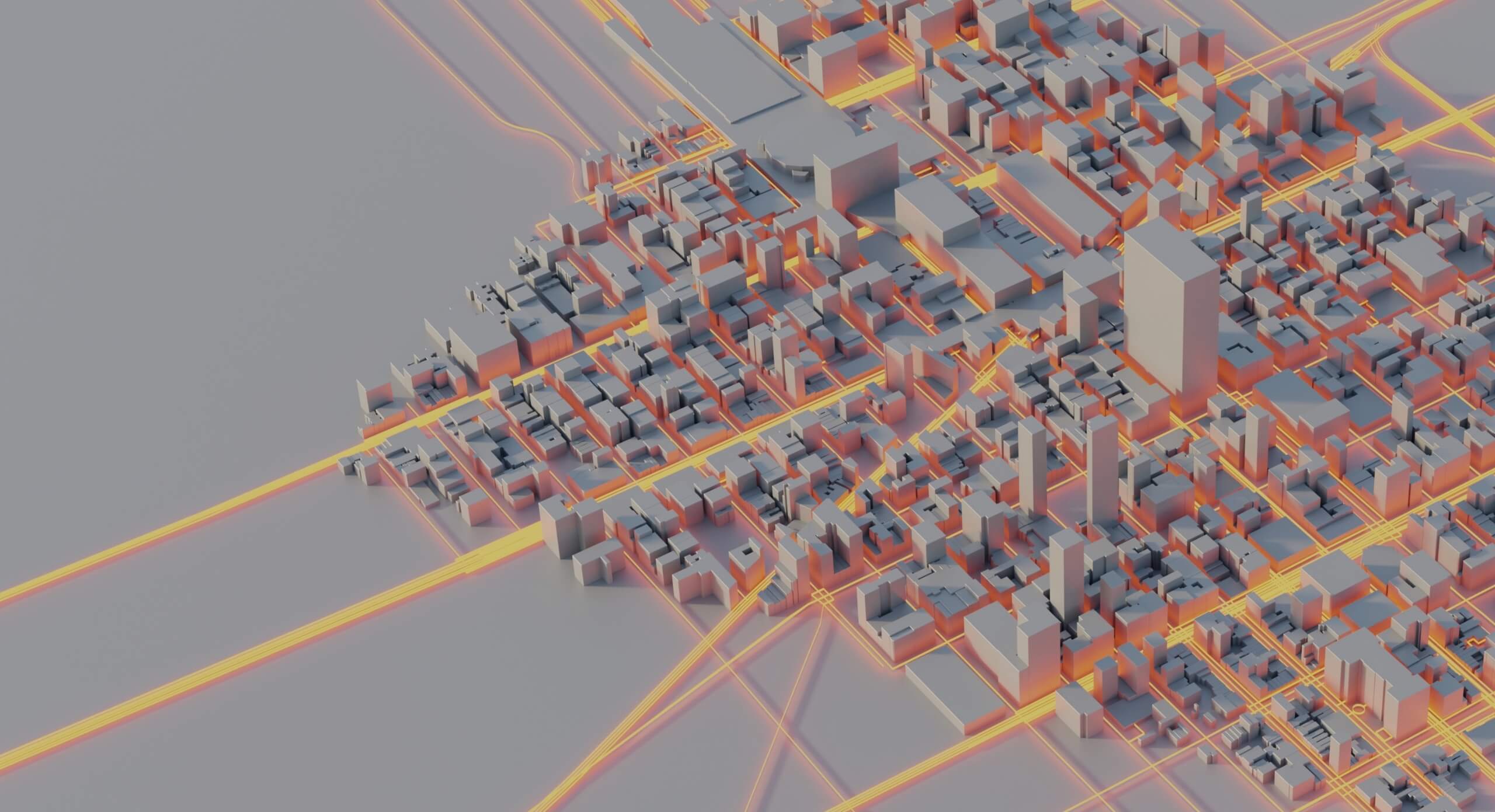
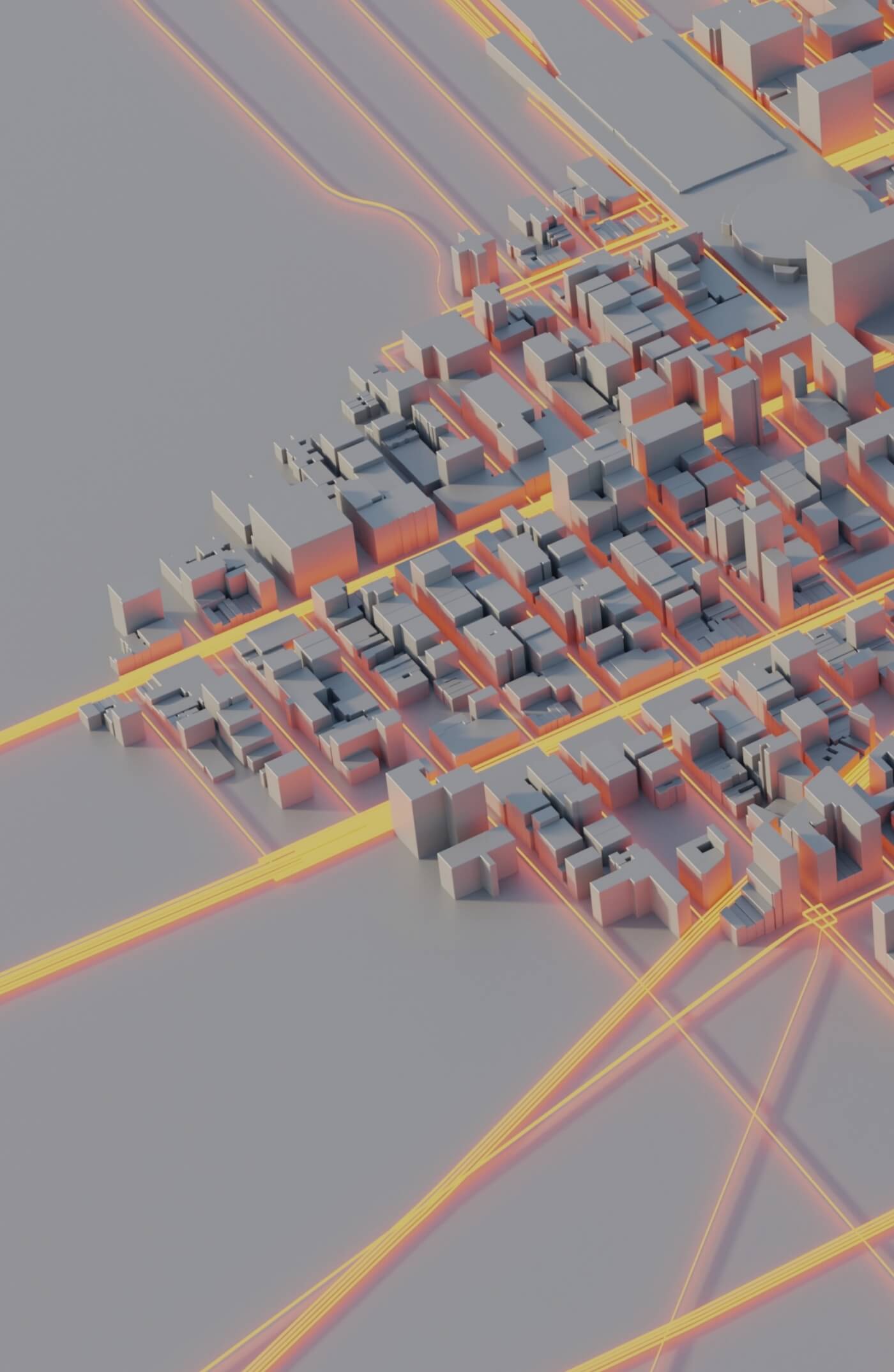
Business
事業のご紹介
Total
Quality
Solutions
トータル・クオリティ・
ソリューション
開発効率の向上に貢献する
信頼性評価・分析/解析技術を
ワンストップで提供しています
私たちは技術者としての情熱と客観的なデータの蓄積を大切にし、製品の「安全」「環境」「快適性」の向上に対して、お客さまに<満足>と<感動>を提供し、社会に貢献できる企業を目指しています。
その始まりは、工場の現場改善、技術指導から。現在は、分析、信頼性試験、試料作製、再現実験、受託研究にいたるまで、「トータル・クオリティ・ソリューション」を提供しています。このトータル・クオリティ・ソリューションにおいては、化学、物理学、金属工学、電気工学、電磁気学といった学術領域をカバーする専門家と、設計開発、生産技術、品質保証など設計や製造の現場に精通した技術者が揃って、問題解決にあたっています。
分析専門の会社や信頼性試験専門の会社など、1つの分野に特化した会社は多くありますが、あらゆる分野を一気通貫で分析・研究をできるのが弊社の強みです。お客さまが直面している不良や故障の真因を追究するのはもちろん、製品の安全・環境・快適性を向上させる改善提案まで踏み込む「力」が、私たちにあります。
幅広い業務の中で蓄積したデータや知見から、電子部品や半導体に対する新しい技術開発にも取り組んでいます。だからこそ、皆さんが普段から耳にするような日本を代表する一流企業が、当社のような中小企業に、技術や品質のことで相談していただけるのだと自負しています。
Some
Works
-
分析
正確・迅速な分析作業で、製品の評価にとどまらず、問題解決までご提案いたします。
MORE -
故障解析
蓄積された高度なノウハウと、最新の設備機器を駆使し、不具合の因果関係を徹底究明します。
MORE -
レーザ加工
超小型・薄型モバイル電子機器に対応。サブミクロンの領域へ、ナノの世界へ。
MORE -
断面研磨/CP加工
月産能力1万個の生産量を誇る研磨センター。実績に基づいた確かな技術力でお届けします。
MORE -
パワーサイクル試験
年間200件以上の受託試験を通じて培ったノウハウと実績。水冷型パワーサイクル試験機も50台準備。
MORE -
信頼性試験
正に製品開発・製造の生命線。高い信頼性を叶えるトータルソリューションをご提案いたします。
MORE -
研究開発(実装技術・基板・表面処理)
分析・検査・実験による情報と技術力で、市場に求められる新工法・新素材をご提案いたします。
MORE
クオルテックでは、
試験や評価の公平性の確保、
およびお客様の要求事項を
満たす体制を整えております。
JNLA認定でお客様から「信頼」
~正確なデータ提供
クオルテックは、独立行政法人 製品評価技術基盤機構(NITE)より産業標準化法試験事業者登録制度 (JNLA)において、ISO/IEC 17025に適合した試験事業所として登録・認定されています。弊社の技術力が国際的に認められ、電子・車載部品の分析・解析・信頼性評価など、数々の試験や検査を受託しております。これからも同認定を維持し、また拡充をはかることで公平性を確保いたします。
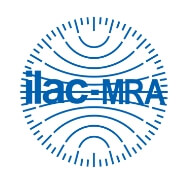
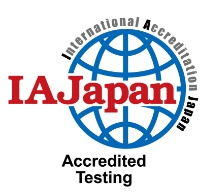

認定区分について
5区分の認定を得ており、
試験方法の名称は以下のとおりです。
区分No. |
試験方法の |
告示に定める |
---|---|---|
215 |
めっき厚さ試験 |
JIS H 8501 |
40 |
絶縁試験 |
JIS C 5012 |
128 |
電気部品 |
JIS C 5012 |
106 |
耐久性・ |
JIS C 5012 |
156 |
自動車部品 |
JIS D 1601 |
弊社の強みは上記に加え、「独立系検査会社」であることと、試験ラインナップが多いことで実現する、幅広いお客様のニーズにワンストップでお応えする「トータル・クオリティ・ソリューション」にあります。中立な第三者が担う評価や試験の重要性の高まりに対して、正確なデータをスピーディに適正価格で提供します。お客様の製品や部品の品質を高め、「安全」「環境」「快適性」の向上に貢献します。
不良ゼロの世界から
「未来品質」の創造へ
不良ゼロの工場や故障ゼロの製品。いわゆる絶対的品質を追求するゼロ思想に加え、空気を浄化しながら走る車、土に還る素材で作られたスマートフォンなど、自然を再生する「未来品質」を備えた製品づくりを、クオルテックの分析・評価、信頼試験、研究開発や微細加工の技術が、トータルにサポート致します。
クオルテックのゼロ思想
(クリックで詳細をご確認できます)
-
0のピラミッド構造
一般的に、下位の概念の目標を達成する前に、上位の概念をターゲットに掲げてしまうと、現場では下位の概念をなおざりにし、期待されるような結果を出せないケースが多く見受けられます。地球に優しいモノづくりというテーマにおいて、0の最高段階である「ゼロ・エミッション」を実現するためにはまず、環境に対する意識改革の徹底と、日頃からの小さなトラブル・ゼロ活動の実践が大切です。小さなトラブルを無視し、日々の改善活動を行わない工場に、不良ゼロ・故障ゼロの実現はありえないし、ストックレス生産など夢のまた夢と言えるでしょう。
環境問題にはまだ新しい分野のテーマが多く、そのため従来の経験の蓄積がなくても、ある程度の成果が期待できる場合があります。しかし現場でトラブルが発生し、製品に問題が発生すると、そうした成果のすべてが水の泡となってしまうことを忘れてはいけません。 -
可能性は必ず実現する!
机の上に置かれているコーヒーカップ。これを悠然と構えている人は、そもそも製造業には向きません。コーヒーカップが床に落下し、壊れ、コーヒーが床に飛び散る状況をすぐに想像し、「危ない!」と咄嗟に叫ぶ人が製造マンとしての最低条件です。いかに可能性が少ないと思われても、こうした行動を取れるようにしておかなくてはなりません。例えば、タバコの灰が灰皿の周りに落ちていることは、その部屋で火災が発生したことと同じだと考えます。こうした訓練を日頃から習慣づけておけば、小さな危険の可能性を見抜く眼力がつき、事故発生を回避できるでしょう。
ゼロを実現するためには、事故や不良を未然に防止する力、即ち小さな可能性でもその結果(先)を読み、すぐに改善に取り組む努力が必要なのです。 -
ハインリッヒの法則
生命保険会社の調査データの分析から生まれたハインリッヒの法則は、一つの大事故が起こる背景には29の中程度の事故が発生しており、さらにその背後には300の小さな事故が存在しているという有名な法則です。人間が関与するさまざまな現象の本質を端的に表現しており、モノづくりの現場にとってはバイブル的存在であります。これに時間軸を当てはめると、大事故は突発的に起こるのではなく、それが発生するまでに小さな事故がいくつも起きているということがわかります。つまり、未来は予測できるのです。事故や不良を絶対に起こしたくない我々にとっては、願ってもない法則だと言えます。
ゼロのモノづくりについての最も基本的な考え方。それは、小さな変化を見逃さない感性を養い、小さなトラブルを一つひとつ改善していけば、必ず大きな目標が達成できるということです。 -
バラツキの要因は
5Mではなく、
1M(Man)だけである従来の品質管理において、不良の原因はバラツキであり、そのバラツキは5つの要因(Material:材料/Method:方法/Machine:機械/Measurement:測定/Man:人間)があるとされています。しかし我々は、不良に直接つながっているバラツキは1M(Man)だけであると考えます。設備が劣化し故障することや材料が変動している場所もあるが、それも事前に受け入れ検査し、保守・点検を確実に実施しておけば、正常な状態に戻すことができます。つまり人間がミスを犯したり、手抜きをしたりしなければ不良発生は防げます。
ゼロのモノづくりは、1M(Man)のバラツキを徹底的に抑えることが重要。そのためにはまず、システムや環境を見直し、誰でもミスを犯さない工場に改革することから始めなければなりません。 -
0のデジタル性と
時間概念全体の不良率の推移グラフを眺めていても、現場の改善には役に立ちません。ゼロ活動にとって重要なのは、不良項目が発生した“1”か、していない“0”かであり、デジタルの世界で言うところの0と1、そしてその間隔(時間)です。ゼロ活動は、1(発生)を完全になくしてしまうことだけではなく、発生する間隔をできるだけ延ばすための活動も含まれます。
Ⅰレベル(1日だけ不良ゼロ達成)・・・作業者の気分
Ⅱレベル(1週間だけ不良ゼロ達成)・・製造責任者の意欲
Ⅲレベル(1ヶ月だけ不良ゼロ達成)・・技術者の努力
Ⅳレベル(3ヶ月だけ不良ゼロ達成)・・製造責任者と技術者のプロのチームワーク
Ⅴレベル(1年間の不良ゼロ達成)・・・素人による基本活動の徹底
Ⅵレベル(10年間の不良ゼロ達成)・・コンピュータ監視による全自動システム?
ゼロのモノづくりは、不良率を下げるのではなく、不良を無くすか、もしくはその間隔を延ばすという考え方(0か1か)しかありません。一般的な製造工程において、工程不良(市場クレームではなく出荷検査前の不良)に着目した場合、“1年間は同じ不良を出さないこと”がゼロ活動を展開する上での重要な目安となります。 -
0は実現可能な
0に分割できる!ある現象は、それを構成している要素に分解できます。また、分解した要素も、さらに下位の概念の要素に分解できます。現象は段階的構造になっています。一方、現象は何かの結果であり、その因果関係を司る要因が存在するし、構成していた要素にも同じ因果関係にある要因があります。つまり現象というのは、時系列的に段階構造に分けられ、上位の現象は下位の要因を排除すれば発生しなくなります。因果関係は直接的なものだけとは限りません。また一対一の関係だけでなく、統計的因果関係や論理的な因果関係などもあり、下位の要因がすべて関わっている場合もあります。
この考えをゼロのモノづくりに当てはめると、不良・故障ゼロのテーマを徹底的に分解していくと、人に関わる要因は支配可能な状態であり、その問題を排除すればゼロは実現できます。緻密な要因分析とその要因を確実に潰していく地道な取り組みこそがゼロ活動であり、それ以外に道はありません。
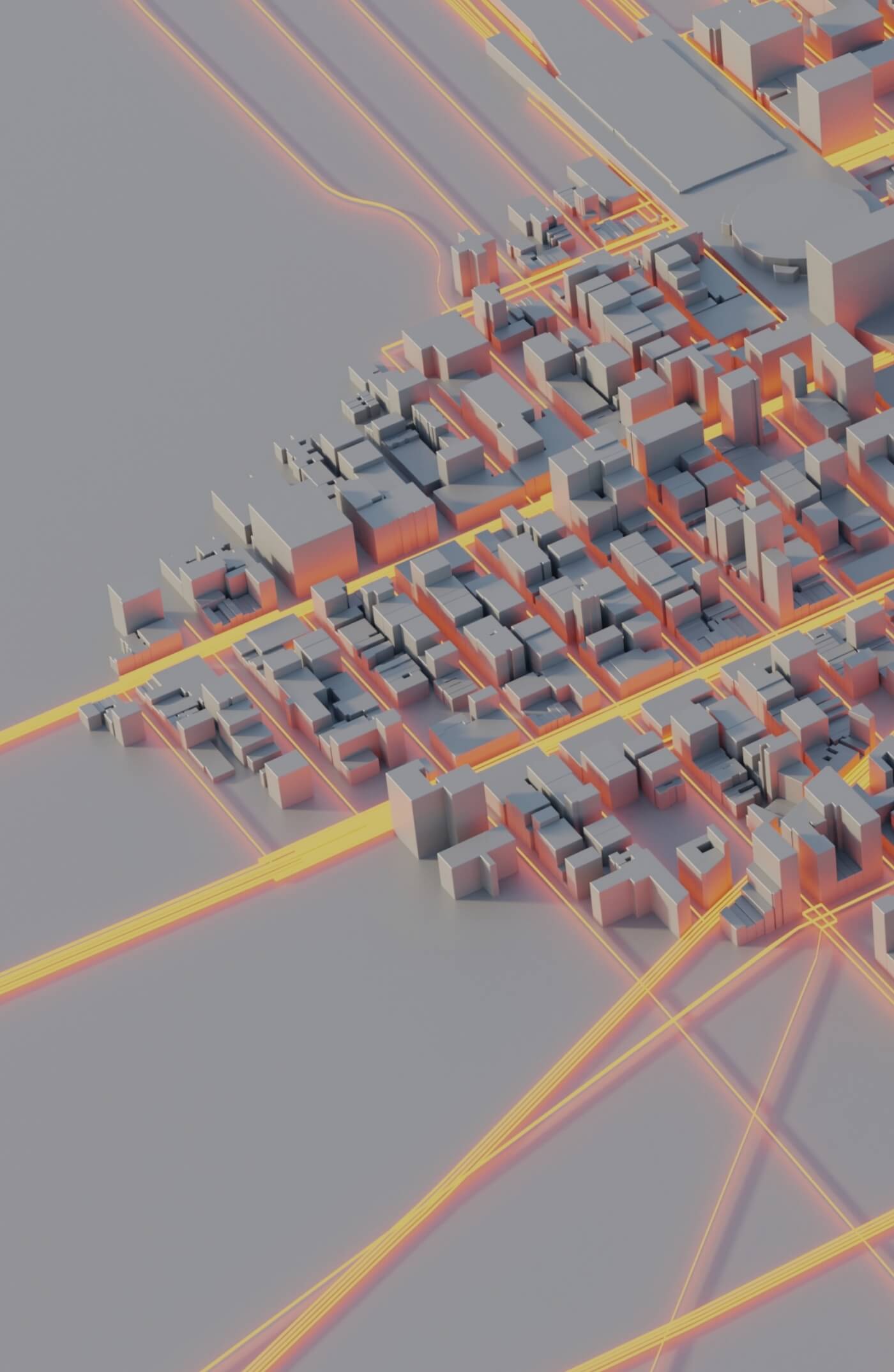